Can Investors Profit From Specialized Industrial Nearshoring?
How Real Estate Investors Can Profit From Specialized Industrial Nearshoring
The world of manufacturing is undergoing a structural realignment. Global trade disruptions, tariff policies, and rising geopolitical tensions have exposed the vulnerabilities of far-flung, just-in-time supply chains. But instead of bringing all production back home, many manufacturers are pursuing a more targeted strategy: nearshoring specialized manufacturing.
This is not about shifting textile factories or generic assembly plants. It’s about relocating high-value, high-complexity production closer to end markets. And it’s creating a significant opportunity for real estate investors, especially those holding or developing the right type of industrial space in the Sunbelt, Midwest, and rust belt hubs like Chicago.
This is why experts like Richard Barnett believe specialized manufacturing is the most viable nearshoring candidate, and what types of properties are best positioned to benefit from it.
Why Specialized Manufacturing is the Prime Nearshoring Candidate
1. It’s About Precision, Not Scale
Unlike commoditized manufacturing, specialized manufacturing involves high-mix, low-volume production. These facilities produce things like:
Aerospace components
Electric vehicle parts
Medical devices
Industrial automation systems
Semiconductors or chip packaging modules
This type of production favors proximity to engineering teams, customers, and supply chain partners. It’s less labor-intensive and more capital-intensive, making labor-cost arbitrage far less relevant. Instead, the priorities shift to supply chain speed, IP protection, and product quality.
2. Proximity and Responsiveness Trump Lowest Cost
What these firms need is:
Fast access to U.S. end markets
Skilled labor or technical training ecosystems
Stable infrastructure and regulatory alignment
That’s why you’re seeing more expansions in Monterrey, Northern Mexico, and U.S. interior markets like Chicago, Columbus, Kansas City, and Greenville-Spartanburg. Specialized manufacturers want to be near logistics hubs, airports, and intermodal rail, not just cheap land.
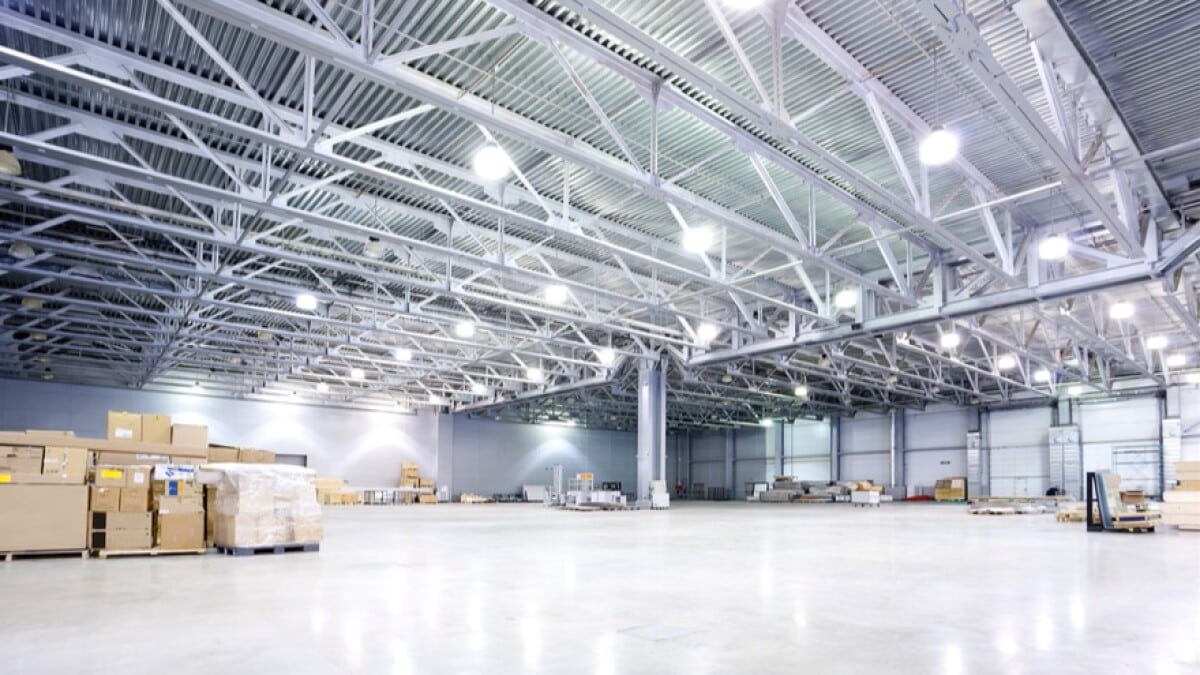
What Real Estate Investors Should Focus On
Investors and developers should be asking: What types of assets and locations will these specialized manufacturers lease or buy? Here’s the breakdown by region and property type.
Modern Mid-Sized Industrial Facilities (Less Than 100,000 SF)
Why: This is the sweet spot for specialized users. It is not too big like e-commerce bulk, but it does not have flex space.
What Tenants Want:
Clear heights of 24’–32′
High power capacity
HVAC-ready shell or conditioned space
Mezzanine or office buildout
Dock and drive-in options
Where to Focus:
Chicagoland’s I-55, I-80, Elk Grove Village, and O’Hare corridors
Cincinnati-Dayton, St. Louis, Milwaukee suburbs
Central Texas, Phoenix, Huntsville, Greenville, SC
In Chicagoland specifically, older Class B/C assets with structural integrity and zoning for light industrial use are being rehabbed into clean-tech or assembly-ready sites. Suburbs like Elk Grove Village, Carol Stream, and Naperville offer a strong mix of infrastructure, workforce, and highway access.
Small-Scale Build-to-Suit or Light Manufacturing Campuses
Why: Many specialized users have custom workflow or equipment needs.
What Tenants Want:
5–20 acre parcels
Room for phased expansion
Utilities to spec (especially 3-phase and high-amperage electrical)
Zoning for light/heavy industrial
Proximity to suppliers, ports, or R&D hubs
Where to Focus:
Periphery of major metros like Indianapolis, Columbus, and San Antonio
Inland logistics zones (e.g. Joliet-Elwood, WI’s I-94 corridor)
Rail-served secondary markets with strong power and incentives
Municipalities compete to attract these tenants, so sites near enterprise zones or manufacturing incentives are especially valuable.
Flex Industrial / R&D-Integrated Facilities
Why: Specialized manufacturers often combine light assembly, prototyping, and R&D in the same footprint.
What Tenants Want:
20,000–60,000 SF with 30–40% office or lab space
Access to engineering talent or academic institutions
Business park settings with strong image and amenities
Where to Focus:
Lake County, IL, DuPage County, North Austin
Ann Arbor, Research Triangle, Tempe-Mesa Gateway area
Libertyville or Lincolnshire for firms serving suburban Chicago medtech clusters
This area is where older suburban office/flex products can be repositioned as “hybrid innovation space” for precision manufacturers and OEM suppliers.
Facilities With Heavy Power or Utility Infrastructure
Why: High-tech manufacturers increasingly need major power loads, especially in the battery, medical device, or microchip packaging sectors.
What Tenants Want:
Sites with existing 2,000+ amps of power
Utility redundancy (dual feeds, backup gen)
High-speed fiber
Where to Focus:
Legacy manufacturing towns (Rockford, South Bend, Peoria) with existing utility capacity
Midwestern towns near data centers and EV investments
Old steel towns with industrial zoning and brownfield sites ready for rehab
If you have an asset with embedded infrastructure, even if it’s cosmetically dated—you may be holding a diamond in the rough for today’s specialized tenant.
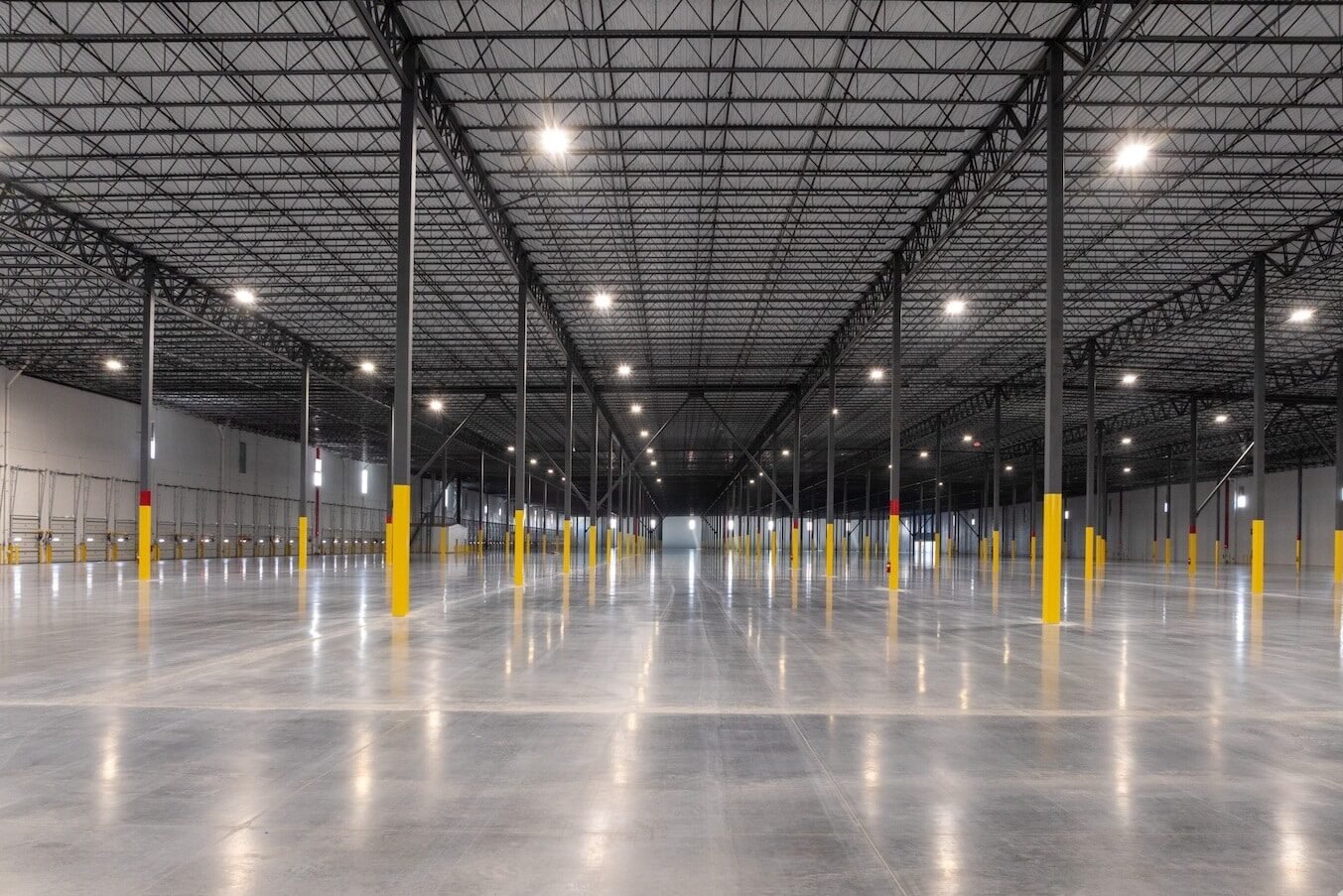
What Makes the Midwest and Chicagoland Especially Attractive
Chicagoland is a logistics nerve center—with six Class I railroads, O’Hare International Airport, and access to I-55, I-80, I-88, and I-90. This makes Chicago a prime target for nearshoring tenants. But unlike e-commerce users who want 500,000+ SF boxes, specialized manufacturers want smaller, more functional spaces near their workforce and suppliers.
Key local advantages:
Diverse Labor Force: From engineering grads to CNC technicians, Chicagoland offers the full talent stack.
Aging Inventory = Opportunity: Many older properties with heavy power and industrial zoning can be repositioned for today’s users.
Proximity to End Markets: Specialized manufacturers serve Tier 1 suppliers, medical networks, or aerospace hubs—many within a few hours’ drive.
Markets like Elk Grove Village, Bensenville, Addison, and Waukegan have proven especially sticky for precision manufacturing users. Lake County continues to see demand from medtech and clean energy manufacturing tenants, while South Suburban locations are attracting companies looking for scale and incentives.
Investor Takeaways
If you’re a real estate investor looking to capitalize on nearshoring demand from specialized manufacturers, here’s how to position:
Prioritize assets under 100,000 SF with flexibility for light production and office/lab integration
Focus on infill submarkets near labor and transit infrastructure
Target power-rich properties or sites with entitlements and utilities ready
Don’t overlook B/C assets—especially if the bones are solid and zoning is favorable
Be early in supply-constrained submarkets where new industrial isn’t being built at scale
Remember: these tenants stay longer, invest more in their spaces, and value proximity to both workforce and logistics. If you have or can develop the right kind of facility in the right location, you’re not just following a trend. You’re capturing the most durable industrial space demand in the next decade.